Dispersants are used to disperse various powders in solvents in a reasonable manner, and to stably suspend various solids in solvents (or dispersions) through certain charge repulsion principles or polymer steric hindrance effects. Dispersants are surfactants that have two opposite properties, lipophilicity and hydrophilicity, in their molecules. They can evenly disperse solid and liquid particles of inorganic and organic pigments that are difficult to dissolve in liquids.
Dispersants are generally divided into two categories: inorganic dispersants and organic dispersants. Commonly used inorganic dispersants include silicates (such as water glass) and alkali metal phosphates (such as sodium tripolyphosphate, sodium hexametaphosphate and sodium pyrophosphate, etc.). Organic dispersants include triethylhexyl phosphate, sodium dodecyl sulfate, methyl amyl alcohol, cellulose derivatives, polyacrylamide, gum, fatty acid polyethylene glycol esters and polyethers, as well as organic silicones and silicone oils.
In mineral processing, dispersants are a type of regulator used in conjunction with collectors, foaming agents or selective flocculants. Dispersants are used to make collectors or flocculants interact better with different minerals to achieve the purpose of sorting. It is generally used to disperse ore mud so that the selected minerals can be effectively separated from the gangue. For example, when selecting kaolin, in order to remove quartz and impurity minerals such as iron and titanium, dispersants such as sodium hexametaphosphate are added to make the kaolin highly suspended and stable. Then, selective flocculants are added to make one of the minerals (kaolin or impurity minerals) form flocs and settle, while the other is still fully dispersed, thereby achieving sorting and improving the grade and natural whiteness of kaolin concentrate. In the flotation process of sulfide ore, an appropriate amount of water glass is used as a dispersant to disperse the gangue mud, so that the sulfide ore and the reagent can interact better, float out of the slurry, and improve the grade of the concentrate.
The amount of dispersant should be moderate. Excessive dispersant will cause the loss of the selected mineral, or it will not have a dispersing effect, but an inhibitory effect. In addition to being used in the mineral processing industry, dispersants are also widely used in light industry, food, chemical industry and other industries.
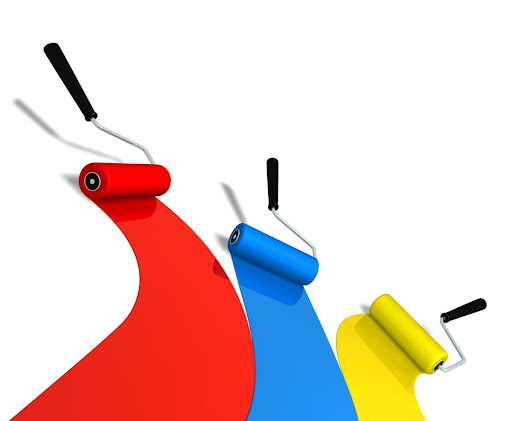