Dispersant is a surfactant with two opposite properties, lipophilicity and hydrophilicity, in the molecule. It can evenly disperse the solid particles of inorganic and organic pigments that are difficult to dissolve in liquids, and at the same time prevent the …
Read More
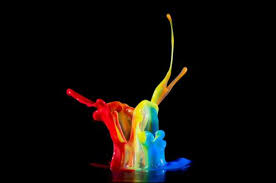