The main function of the wetting agent is not to be used in the pigment grinding process. Its main function is to reduce the surface tension of the pigment system, so that the pigment can achieve good adhesion and leveling properties during the coating process on the substrate. Therefore, There is a certain difference between wetting agents and wetting and dispersing agents.
Read More
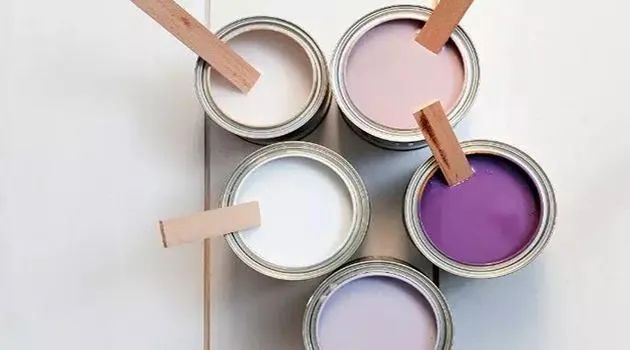